Forschungsprojekt entwickelt neue Technologie zur Fahrhöhenmessung bei Nutzfahrzeugen
Die Scemtec Sensor Technology GmbH, die plastec Kunststofftechnikum Oberberg GmbH und die TH Köln entwickeln daher in dem gemeinsamen Projekt „NIVEAUsens“ ein neuartiges Sensorsystem, das wenig anfällig gegenüber Außeneinflüssen ist: es basiert auf der Messung eines Magnetfeldes in der Luftfederung und soll verschleiß- und wartungsfrei sein.
Beim Einsatz von Nutzfahrzeugen ist eine Regelung der Fahrhöhe unerlässlich – bei landwirtschaftlichen Maschinen, um auf unebenem Grund einen stets waagerechten Aufbau sicherzustellen; bei Transportern, um bei veränderter Beladung einen konstanten Abstand zwischen Karosserie und Fahrbahn zu gewährleisten. „Zumeist werden Fahrhöhenregulierungen mit einem freiliegenden Gestänge eingesetzt. Dieses ist Einflüssen wie Temperatur, Feuchtigkeit und Steinschlag ausgesetzt und muss regelmäßig gewartet bzw. ausgetauscht werden“, erläutert Scemtec-Geschäftsführer und NIVEAUsens-Projektleiter Joachim Uhl.
Die Projektpartner setzen stattdessen auf ein berührungsloses Sensorsystem, das innerhalb der Gummischutzhülle der Luftfederung, dem sogenannten Balg, verbaut ist. Dabei erzeugt ein Sender am Deckel des Balgs ein starkes Magnetfeld. Ein am Boden des Balgs verbauter Empfänger auf Höhe der Achse misst die Magnetfeldstärke. Wird die Luftfederung durch eine Belastung zusammengestaucht oder entspannt sie sich, ändert sich der Abstand zwischen Deckel und Boden und damit zwischen Sender und Empfänger. Aus der gemessenen Feldstärke soll dann der aktuelle Abstand zwischen beiden Bauteilen und somit auch die aktuelle Fahrhöhe rekonstruiert werden.
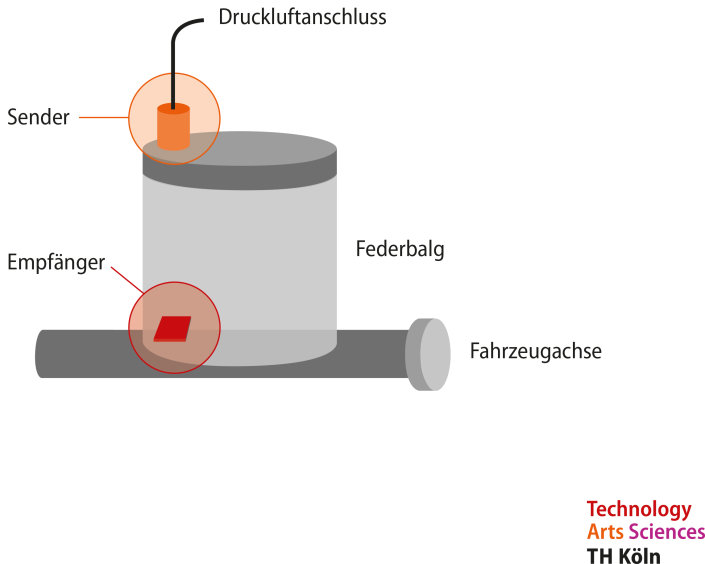
Sensortechnik schützen
Innerhalb des Balgs herrschen Bedingungen, die für die empfindliche Sensortechnik zum Problem werden könnten. Daher entwickelt die plastec Kunststofftechnikum Oberberg GmbH ein spezielles Schutzgehäuse. „Unsere Herausforderung ist es, ein kleines und leichtes Bauteil bereitzustellen, das einerseits günstig in der Herstellung ist, andererseits aber den großen Vibrationskräften wiedersteht, die im Achsbereich herrschen“, erläutert Geschäftsführer Michael Sanin. Damit die Funktion von Sensoren und Antennen dauerhaft sichergestellt ist, müsse zudem eine besonders sichere Abdichtung des Federbalgs konstruiert werden, die das Eindringen von Staub, Öl und Schmutz zuverlässig verhindert.
Tests im Sub-Millimeter-Bereich
Das Institut für Allgemeinen Maschinenbau der TH Köln unterstützt plastec bei der Erforschung, Entwicklung und Prüfung der optimalen Kunststoffmaterialien und führt bei den ausgewählten Materialien Belastungstests und Stabilitätsuntersuchungen durch. „Zudem bauen wir einen neuartigen Prüfstand auf, mit dem das ganze System fahrdynamischen Untersuchungen unterzogen wird. Zur Simulation der realen Arbeitssituation bei Land- und Nutzmaschinen müssen große Massenbewegungen und Kräfte simuliert werden. Dabei werden wir diese hohen Massen im Sub-Millimeter-Bereich aufeinander zubewegen und abbremsen, um die Funktionalitäten und die Genauigkeit der Sensorsystem-Prototypen exakt zu bestimmen“, sagt der Laborleiter Prof. Dr. Axel Wellendorf.
Geplante Vorteile: weniger Verschleiß und Wartung, längere Lebensdauer
Da die Messtechnik innerhalb des Federbalgs verbaut ist, werden die Messungen nicht durch Temperaturschwankungen, Eisbildung, Verschmutzung, Stöße oder Vibrationen gestört. Zudem befinden sich im Balg keine Metallteile, die das Magnetfeld beeinflussen könnten. „Die verwendete Technologie wird berührungslos arbeiten. Daher soll sie wartungs- und verschleißfrei sein. Das kann die Lebenszeit der Federungssysteme in Land- und Nutzfahrzeugen um ein Vielfaches erhöhen“, prognostiziert NIVEAUsens-Projektleiter Uhl.
Das Forschungs- und Entwicklungsprojekt NIVEAUsens wird bis Mitte 2021 über das Zentrale Innovationsprogramm Mittelstand (ZIM) des Bundesministeriums für Wirtschaft und Energie gefördert.
März 2020