Kunststoffstrang statt gefräster Facette
Neue Methode zur Verbindung von Brillenglas und Brillenfassung: Eine elastische Verbindung von Brillenglas und Brillenfassung statt der starren Verbindung durch Facette und Nut – mit diesem Konzept haben Absolventen der TH Köln das Unternehmen Shape Engineering GmbH gegründet.
Download
Die Pressemitteilung vom 28. April 2017 als PDF lesen.
Bei ihrer patentierten Methode zur Brillenglasbearbeitung wird Material nicht nur weggefräst, sondern auch in einer Art 3D-Druck-Prozess hinzugefügt. Damit vereinfachen die Gründerinnen und Gründer den Fertigungsprozess, erhöhen die Sicherheit und erweitern den Gestaltungsspielraum von Brillendesignern. Gefördert werden sie durch das Programm EXIST-Forschungstransfer des Bundesministeriums für Wirtschaft und Energie.
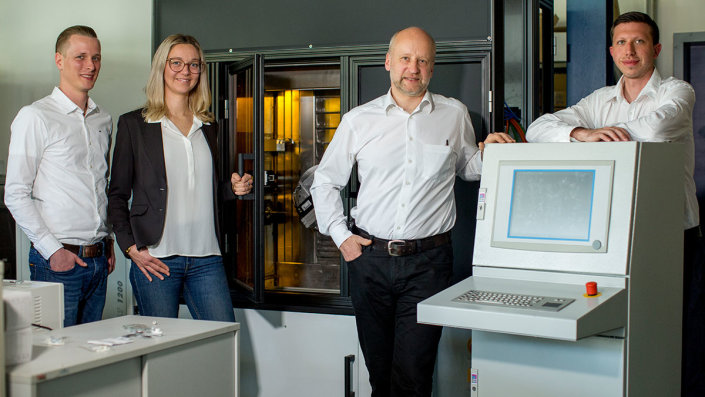
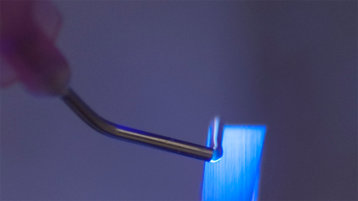
"Mit unserem Verfahren wollen wir die Brillenfertigung revolutionieren und neue Qualitätsmaßstäbe setzen. Anstatt eine Facette aus dem Brillenglas herauszuarbeiten, tragen wir auf den Glasrand einen dünnen Kunststoffstrang auf, der die Funktion der Facette übernimmt. Als Kunststoff nutzen wir ein Photopolymer, das unter UV-Licht in Sekunden aushärtet. So erreichen wir eine stabile und spannungsfreie Verbindung von Glas und Fassung", erklärt Geschäftsführer Christian Pöpperl, der das Team der Shape Engineering GmbH zusammen mit der kaufmännischen Leiterin Carina Kühl und dem Entwicklungsingenieur Simon Nijmeijer bildet.
Weitere Informationen
In ihren ersten beiden Geschäftsjahren wollen die Jungunternehmer die Technologie vom Prototypen zum vermarktungsfähigen Produkt weiterentwickeln und die Zusammenarbeit mit Investoren und strategischen Partnern intensivieren. Zudem akquirieren sie Entwicklungsaufträge aus der augenoptischen Industrie. In dieser Zeit werden sie weiterhin Räumlichkeiten der TH Köln nutzen. "Wir möchten nicht nur in der Gründungsphase, sondern dauerhaft mit unserer Hochschule verbunden bleiben und streben auch langfristig Forschungskooperationen an", so Pöpperl.
Bildmaterial
Bildmaterial zur honorarfreien Verwendung bei Copyright-Angabe stellen wir Ihnen gerne zur Verfügung. Bitte wenden Sie sich dazu an pressestelle@th-koeln.de.
Optimierter Fertigungsprozess, verbesserte Sicherheit, Freiheiten für Designer
Das neu entwickelte Verfahren hat für Brillenhersteller mehrere Vorteile. So vereinfacht es die Montageprozesse und erhöht die Passraten zwischen Brillenglas und Brillenfassungen. Dadurch sinken die Fertigungskosten bezogen auf die reine Randbearbeitung des Brillenglases um bis zu 50 Prozent. Außerdem verringert sich die Gefahr des Glasbruchs, sagt Pöpperl: "Um zu prüfen, ob die Gläser auch sicher in der Fassung halten, haben wir einen Belastbarkeitstest durchgeführt. Während die konventionell bearbeiteten Gläser brachen, wurden die Gläser mit der Polymerfacette ohne Beschädigung aus der Fassung gedrückt. Danach konnte das Glas einfach wieder eingesetzt werden."
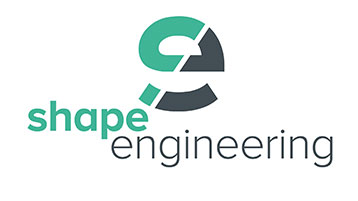
Bei der Fertigung von Nylorbrillen muss nicht wie bislang eine Rille für den Nylorfaden in das Glas gefräst werden. Stattdessen werden zwei Stege aus Kunststoff auf das Glas aufgetragen, die den Faden halten. Der Glasrand wird auf diese Weise nicht geschwächt und die minimal benötigte Randdicke kann reduziert werden, was auch das Glasgewicht senkt. Für Brillendesigner ergeben sich durch die neue Methode deutlich größere Gestaltungsmöglichkeiten, da sie nun Strukturen entwickeln können, die nicht mehr aus dem Glas selber herausgearbeitet werden müssen, sondern mit sehr wenigen Einschränkungen auf den Glasrand aufgetragen werden. "Besonders interessant ist die Entwicklung von Sportfassungen oder die Gestaltung von Nasenpads. Aber auch Schmuckelemente können sehr einfach in das Design integriert werden", so Pöpperl.
Die Firmengründung beruht auf dem Forschungsprojekt "New Edging Technology", das unter der Leitung von Prof. Dr. Jörg Luderich zwischen 2011 und 2014 am Institut für Produktentwicklung und Konstruktionstechnik der TH Köln bearbeitet und erfolgreich abgeschlossen wurde. Prof. Luderich fungiert heute als Mentor des Gründerteams.

gefördert durch:
April 2017