Hybrid-Antrieb für Holzhacker spart 20 Prozent Treibstoff
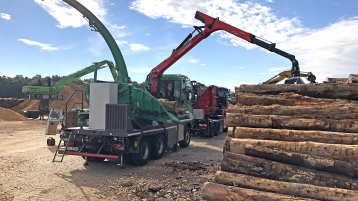
Holzhackschnitzel als alternativer Brennstoff für Industrie und Privathaushalte werden in der Regel mit mobilen, dieselbetriebenen Hackern hergestellt. Diese halten während des Arbeitsvorgangs meistens nicht ihren optimalen Betriebspunkt und verbrauchen so mehr Treibstoff als nötig.
Um das zu ändern, hat ein Team vom Kölner Labor für Baumaschinen der TH Köln unter Leitung von Prof. Dr. Alfred Ulrich einen Hacker zum Hybrid-Fahrzeug weiterentwickelt. Im Vergleich mit einem herkömmlichen Modell können so 20 Prozent Diesel eingespart werden bei gleichzeitiger Steigerung der Arbeitsleistung.
Download
Die Pressemitteilung vom 11. November 2020 als PDF lesen.
„Hackschnitzel werden aus Stämmen, Wurzeln oder Ästen gewonnen. Deshalb ändert sich permanent die Beschaffenheit und Härte des Holzes, das in den Holzhacker eingebracht wird. Die Motoren des Hackers laufen daher ständig mit hoher Leistung, um im Bedarfsfall auch dicke Stämme sofort verarbeiten zu können, und sind weit weg von ihrem optimalen Betriebspunkt. Damit verbrauchen sie mehr Diesel als eigentlich benötigt wird, was die Umweltbelastung erhöht“, erläutert Teamleiter Dirk Niederberghaus die Ausgangslage. Um dieses Problem anzugehen, entwickelte das Team des Labors das Konzept für einen Hybrid-Hacker und baute eine Maschine entsprechend um.
Bildergalerie
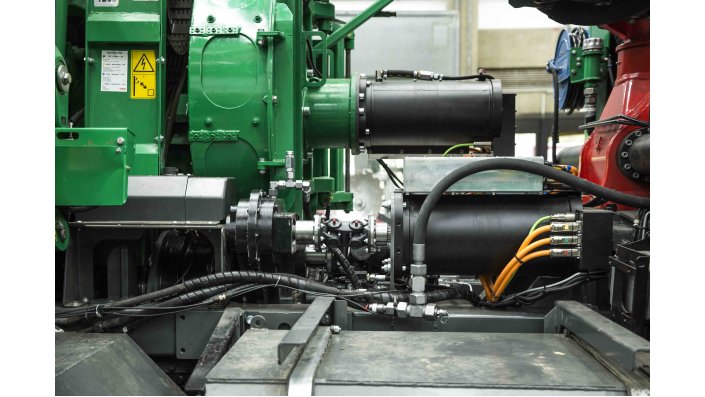
Neben dem dieselbetriebenen Motor, der sowohl den LKW-Antrieb als auch das Hackgerät mit Energie versorgt, verfügt das Fahrzeug nun zusätzlich über einen elektrischen Antrieb (rechts unten). (Bild: Heike Fischer/TH Köln)

Der Hybrid-Antrieb (links) unterstützt den Hacker, wenn mehr Leistung gebraucht wird als der Verbrenner im optimalen Betriebspunkt bereitstellen kann. (Bild: Heike Fischer/TH Köln)
Elektromotoren ergänzen Verbrenner
Neben dem dieselbetriebenen Motor, der sowohl den LKW-Antrieb als auch das Hackaggregat mit Leistung versorgt, verfügt das Fahrzeug nun zusätzlich über drei Elektromotoren mit insgesamt rund 200 kW Leistung. Der Verbrenner-Motor läuft während des Hackvorgangs möglichst nah an seinem optimalen Betriebspunkt. Wird für den Hackvorgang nur wenig Leistung benötigt – weil etwa gerade Kronenholz verarbeitet wird – lädt die überschüssige Energie 13 sogenannte Superkondensatoren auf. Diese speichern elektrische Energie und können sehr schnell ge- und entladen werden.
Benötigt das Zerhacken eines dicken Stamms mehr Leistung als der Verbrenner im optimalen Betriebspunkt bereitstellen kann, schalten die Elektromotoren in den sogenannten Boost-Modus und liefern durch das Entladen der Superkondensatoren die Differenzleistung zu. „Der Boost-Modus springt automatisch an, wenn mehr Kraft gebraucht wird. Die Maschinenführerinnen und -führer haben aber auch die Möglichkeit, den Boost manuell dazu zu schalten, um bestimmte Arbeitsprozesse zu beschleunigen“, sagt Niederberghaus.
Versuch belegt Treibstoffersparnis
In einem finalen Test verglichen die Projektpartner ihren umgebauten Hacker mit einem baugleichen Modell mit herkömmlichen Antrieb. Als Testmaterial dienten Baumstämme vergleichbarer Härte, Durchmesser und Beschaffenheit. „Insgesamt verarbeiteten die beiden Hacker rund 100 Festmeter Holz. Unser umgebautes Modell verbrauchte dabei rund 20 Prozent weniger Diesel bei gleicher Qualität der Hackschnitzel und gesteigerter Arbeitsleistung, bezogen auf die Hackschnitzel pro Zeiteinheit“, sagt Niederberghaus.
Das Forschungsprojekt EnGie-Hacker ist eine Kooperation des Kölner Labor für Baumaschinen (KLB) der TH Köln, der Jenz GmbH Maschinen- und Fahrzeugbau, der Antriebstechnik Roth GmbH und der Vemac GmbH. Es wurde über drei Jahre im Rahmen der Initiative EFRE.NRW in Zusammenarbeit mit dem Ministerium für Wirtschaft, Innovation, Digitalisierung und Energie des Landes Nordrhein-Westfalen und dem europäischen Fonds für regionale Entwicklung der Europäischen Union gefördert.
November 2020