AutoProStoffe - Vernetzung und Automatisierung von Produktionsabläufen
Moderne Landwirtschaft ist immer häufiger durch große Datenmengen getrieben und die mangelnde Interoperabilität erfordert eine sorgfältige Auswahl von Maschinen, Sensoren und Datenverarbeitungsplattformen und erschwert die Anpassung dieser Systeme an die spezifischen Bedürfnisse des einzelnen Landwirts. Das Horizon-2020-Projekt „ATLAS“ strebt danach, diese Einschränkungen zu überwinden.
Kurzbeschreibung
In der Wertschöpfungskette von mineralischen Rohstoffen lassen sich wiederkehrende Schnittstellen zwischen den einzelnen Arbeitsschritten erkennen:
Es wiederholt sich das Aufnehmen des Rohstoffs mit einem Ladegerät, das Verladen auf ein Transportgerät sowie das Transportieren des Rohstoffs. Durch fehlende Automatisierung dieser Arbeitsfunktionen wird das Optimierungspotenzial der gesamten Wertschöpfungskette begrenzt. Des Weiteren kann eine intelligente Vernetzung der Prozessteilnehmer, auf Grund fehlender Netzwerkstruktur für Anwendungen im mobilen Bereich, derzeit nicht umgesetzt werden.
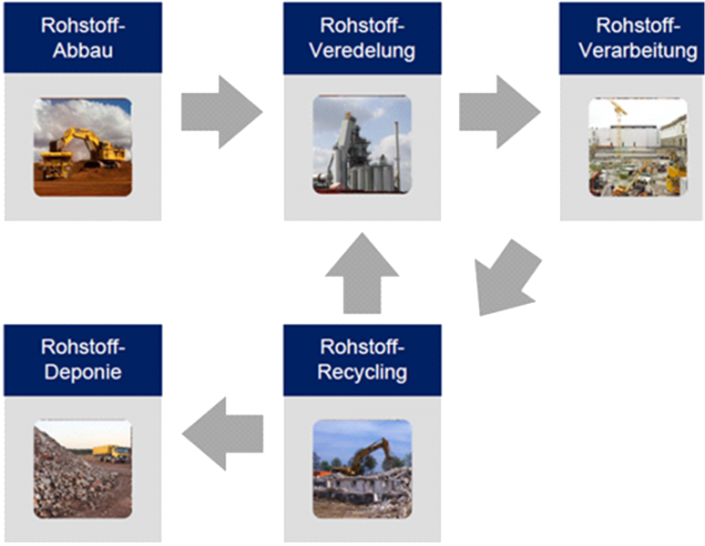
Technische Ziele des Projekts
Das Ziel des Projekts ist es, einzelne Arbeitsfunktionen zu erfassen und zu automatisieren. Außerdem sollen alle Teilnehmer der Prozesskette über eine intelligente Vernetzung verfügen, die es ermöglicht, einzelne Prozesse oder Teilnehmer zu steuern.
Konkret umgesetzt werden diese Maßnahmen durch:
- Lastabhängige Schaufelreglung
Die Aufnahme von Rohstoffen mit einem Ladegerät ist ein komplexer Prozess und soll, zur Entlastung des Bedieners, von einer Steuerung übernommen werden. Der dynamische Grabprozess wird dazu mit einem neu entwickelten Ansatz, bei dem über die Druckstütze der Schaufel die Belastung erfasst wird, überwacht.
- Störgrößenkompensiertes Wiegesystem für Ladegeräte
Um das Gewicht prozesssicher erfassen zu können, wird ein Wiegesystem entwickelt, welches die auftretenden Störgrößen mit Hilfe eines modellbasierten Ansatzes erfasst und kompensiert. Dieser Ansatz kann sowohl für Hydraulikbagger als auch für Radlader verwendet werden.
- Vorbeugende Instandhaltung
Zur Vermeidung und Erkennung von Schäden wird das oben beschriebene Wiegesystem genutzt, als auch eine Geometrieerkennung der Löffelschneide an den Ladegeräten. Die Verschleißerkennung wird durch eine modellbasierte Kantendetektion umgesetzt werden. Zusätzlich soll eine Positionsbestimmung der Löffelschneide, den Verschleiß und die Beschädigung der Zähne reduzieren.
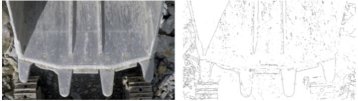
- Intelligente Nahfeldkommunikation/Prozessoptimierung durch Messdatenanalyse
Alle Prozessteilnehmer werden in drei Gruppen zusammengefasst: Ladegeräte, Transportgeräte und Verarbeitungsanlagen. Die Teilnehmer werden Daten untereinander austauschen und können diese den Bedienern mitteilen.
Bestimmte Teilnehmer sollen außerdem eine Schnittstelle zu einer übergeordneten Instanz haben. Diese kann, anhand der erhaltenen Daten, Anweisungen zur Optimierung des Prozesses generieren und an die Teilnehmer senden.

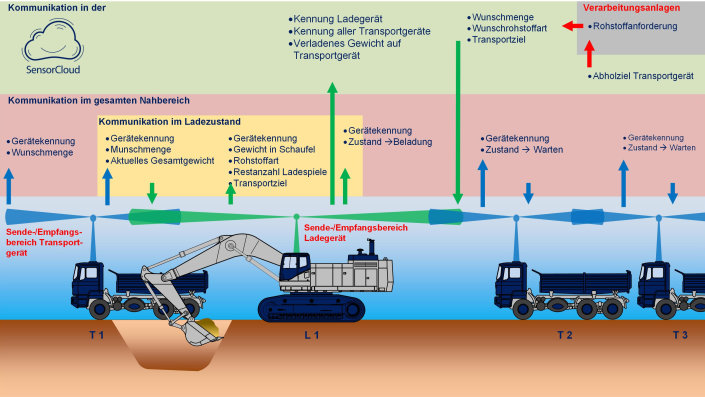
Projektabschluss
Das Projekt wurde im März 2019 erfolgreich abgeschlossen.
Dazu wurden im laufe des Forschungsprojekts die notwendigen Prozessdaten in einer umfangreichen Messkampagne ermittelt und analysiert. Anhand der erhaltenen Daten konnten neue Systeme entwickelt werden, durch die die genannten Ziele umgesetzt wurden. Die entwickelten Systeme konnten in Rahmen von Labor- und praktischen Untersuchungen verifiziert werden.
Durch die parallele Entwicklung eines Baggerprüfstands bestand die Möglichkeit die entwickelten Systeme wie Wiegesystem, Automatisierung von Teilprozessen, Schaufelregelung und vorbeugende Instandhaltung im Labor und in der Praxis umzusetzen. Die Entwicklung einer Nahfeldkommunikation konnte in einem Modellsteinbruch nahe Sundern umgesetzt werden. Damit können relevante Daten zwischen einzelnen Maschinen und der Verarbeitungsanlage ausgetauscht werden, um so den Prozess live zu analysieren und aktiv in den Prozess einzugreifen und zu optimieren.
Zusammen mit den Forschungspartnern konnten so zukunftsweisende Systeme im Bereich der Rohstoffgewinnung in Richtung Industrie 4.0 entwickelt werden.

Auf einen Blick
Kategorie | Beschreibung |
---|---|
Forschungsprojekt | AutoProStoffe - Vernetzung und Automatisierung von Produktionsabläufen in der Gewinnung, dem Transport sowie der Weiterverarbeitung von mineralischen Rohstoffen |
Leitung | Prof. Dr. Alfred Ulrich |
Institut | Kölner Labor für Baumaschinen (KLB) am Institut für Bau- und Landmaschinentechnik (IBL Köln) |
Projektpartner | Völkel Mikroelektronik GmbH, TPA Gesellschaft für Qualitätssicherung und Innovation GmbH, Langendorf GmbH |
Fördermittelgeber | Europäische Union in Verbindung mit dem Ministerium für Wirtschaft, Energie, Industrie, Mittelstand und Handwerk des Landes Nordrhein-Westfalen |
Laufzeit | 2016 - 2019 |