Forschungsprojekt DrEMopt
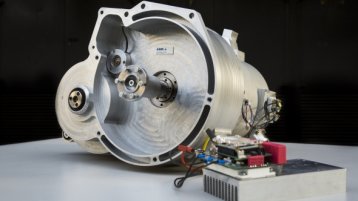
Effizienzuntersuchung einer Doppelt rotierenden Elektrischen Maschine (DrEM) für den Einsatz in Hybridfahrzeugen.
Aufbauend auf dem Forschungsprojekt DrEM-Hybrid ist in Kooperation mit der Firma Continental AG das Herzstück des DrEM-Hybridantriebes, die Doppelt rotierende Maschine, hinsichtlich seiner Effizienz untersucht worden.
Mit den aus der Vermessung erhaltenen Ergebnissen ist danach das Fahrzeug mithilfe eines Simulationstools nachgebildet worden. Mit diesem Fahrzeugmodell konnte eine deutliche Effizienzsteigerung im Vergleich zu einer konventionellen Antriebsstruktur nachgewiesen werden.
So zeigte die neuartige Antriebsstruktur einen Verbrauchsvorteil von 2,23 l je 100 km (32,7 %) verglichen mit einem konventionellen Antriebsstrang.
Wirkungsgradkennlinienfeld der DrEM bei nVKM=2.250 1/min (Bild: Rustam Nagaev, TH Köln)
Auf einen Blick
Kategorie | Beschreibung |
---|---|
Forschungsprojekt | Vermessung einer doppelt rotierenden elektrischen Maschine (DrEM), Modellbildung und Simulation eines DrEM-Hybridfahrzeugs mit verschiedenen Fahrzyklen |
Leitung | Prof. Dr.-Ing. Andreas Lohner |
Fakultät | F07 |
Institut | Institut für Automatisierungstechnik |
Beteiligte | Prof. Dr.-Ing. Andreas Lohner, Rustam Nagaev B.Sc. |
Projektpartner | Continental Automotive Cross Divisional Functions |
Fördermittelgeber | Continental Aktiengesellschaft |
Laufzeit | 06.2016 – 12.2016 |
Website |
Funktionsweise der DrEM:
Wie in der Abbildung „Funktionsschaubild der DrEM“ zu sehen ist, besitzt die DrEM – im Gegensatz zu einer konventionellen Maschine – keinen Stator sondern zwei Rotoren. Der Rotor (1), an dem die Schleifringe befestigt sind, wird fest mit der Kurbelwelle des Range Extenders verbunden. Der Rotor (2) mit den Permanentmagneten wird über eine Getriebeübersetzung und das Differential an die Vorderräder gekoppelt. Durch eine geeignete Bestromung der Maschine kann damit die Drehzahl des Verbrennungsmotors von der Fahrzeuggeschwindigkeit entkoppelt werden. Dies ermöglicht eine Verschiebung des Arbeitspunktes in den verbrauchsoptimierten Drehzahlbereich des Verbrennungsmotors.
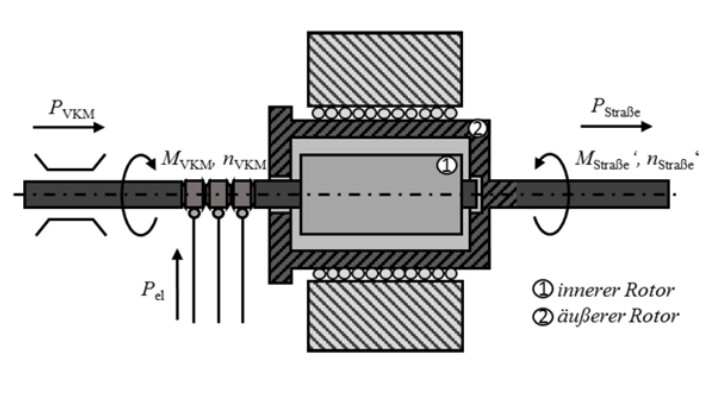
Prüfstandsaufbau:
Wie in der Abbildung des schematischen Prüfstandsaufbaus zu sehen ist, ist zur Nachbildung der Fahrzeugdynamik und des Range Extenders je ein Elektromotor eingesetzt worden. Somit konnte jeder zur Konstruktion des Effizienzkennlinienfeldes benötigte Arbeitspunkt vermessen werden. Mit Hilfe zweier hochgenauer Messflansche wurden sowohl das Drehmoment am inneren Rotor, als auch das Drehmoment, das an den Rädern anliegt, gemessen und via CAN an die übergeordnete Steuerung zur weiteren Verarbeitung gesendet. Durch den Einsatz eines multikanaligen Präzisionsleistungsmessgerätes konnten sowohl die AC- als auch die DC-Leistung des Leistungsumrichters ermittelt werden, was neben der Ermittlung der elektrischen Leistung der DrEM gleichzeitig eine Effizienzbestimmung der Leistungselektronik ermöglicht.
Als übergeordnete Steuerung wurde eine Rapid Prototyping Steuerung eingesetzt, welche eine schnelle und einfache Integration aller Komponenten als auch das zügige Implementieren des Messverfahrens erlaubte.
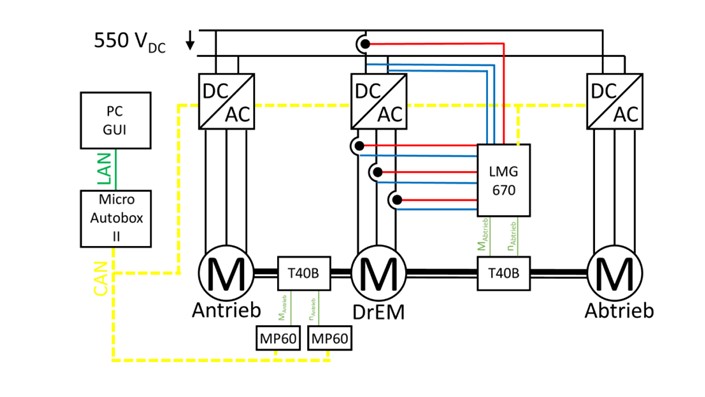
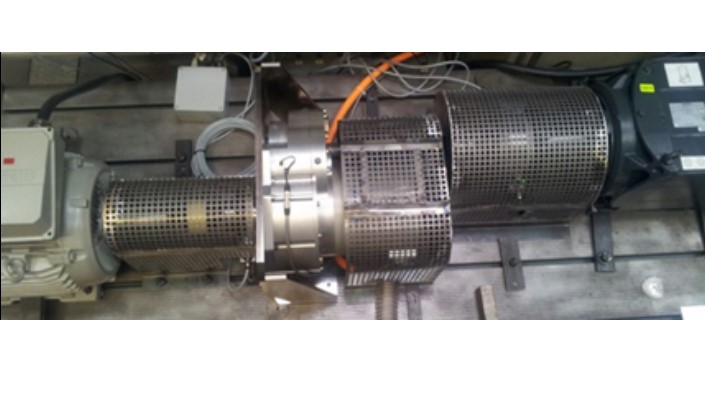
Links: Elektromotor zur Simulation des Range Extenders (Antrieb)
Mitte: DrEM (Prüfling)
Rechts: Elektromotor zur Simulation der Fahrzeugdynamik (Abtrieb)